Digital Lean boards for visual daily management
By bringing together the power of visualization from Lean production with the advantages of the digital world, we have created a platform where you can tailor everything from daily management boards to improvement and KPI boards.
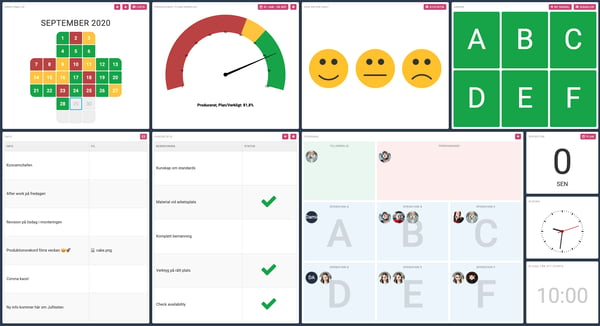
More value for less work
The concept of Lean production was first mentioned in a study carried out by MIT and was used to describe Toyota's unique work strategy, the so-called Toyota Production System. The Japanese company, during the post-war period, had developed a slim and streamlined way of working to make the production flow, minimize waste of resources and create more value for less work.
The world soon realized its benefits and the concept spread internationally. Today, Lean production is a widespread approach that affects everything from leadership to designing work tools and processes. Lean is widely applied in several industries - in factories as well as in healthcare, administration and real estate.
Visualization and Performance control system
One of the main principles of Lean production is to dare to highlight setbacks and problems in order to be as effective as possible. You often talk about the Japanese lake; by lowering the water level the problems are made visible. The concept means that we do not always allow ourselves to see the problems, but by visualizing they reveal themselves.
And that is exactly what our digital lean boards are about. By visualizing information in the right way, you can quickly form an objective view at first glance and take care of the problems that occur. Each board is tailor-made to help you both streamline the dissemination of information and deliver customer value in a smarter way.
Below are examples of some of the solutions we can create for your business. By implementing all types of boards, you get a complete performance control system for your business.
SQCDP board for shop floor management
The SQCDP board (or Gemba board) is an effective tool for visualizing how the different teams perform under different key figures in the areas of Safety, Quality, Cost, Delivery and People. The idea is to drive development work forward by highlighting the development potential that exists in these areas.
The board is a calendar shaped in the letters SQCDP which is marked in green each day the goals are achieved. This gives teams and management a concrete overview of the most important things for the day. At the same time, they can easily follow the progress made in each area.
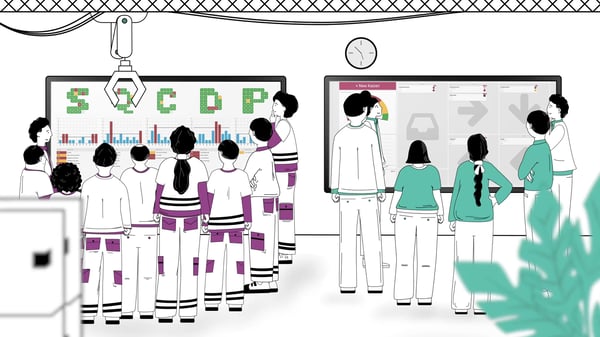
Kaizen board with escalation to the management team
Kaizen is a Japanese concept that means: "continuous improvement", or more specifically to constantly streamline and improve your business. In traditional Kaizen work, one is limited to streamlining only what can be discovered with the naked eye. But with a digital Kaizen template you can go a step further.
A Kaizen board for the management is a form of improvement board that gives you an overview of escalations and delegations between different departments and teams. Around a kaizen board, the management team can gather to, for example, make decisions on escalated issues and ensure that the business is constantly improving. For example, you can follow the entire production chain live to quickly fix issues, or even prevent them from occurring.
Improvement Board
To work with continuous improvement is to strive for a corporate culture where the entire business, from floor shop employees to management, is involved in the continuous development of the business and the processes. An improvement board is an essential part of this work.
With an improvement board, you get help to look at more comprehensive and long-term improvement issues. Each team can submit suggestions from their smartphones at any time and then work together by the board to prioritize them. Whether you want to improve routines, processes or entire strategies, the improvement board is your best friend.
Plan-Do-Check Act, PDCA
The PDCA (Plan do check act) wheel is a well-known methodology used to plan, implement, control and introduce new improvements. With such a board, you can easily track the improvement tasks in the PDCA wheel just as you had done with post-it notes on a whiteboard. The process usually goes something like this:
- Identify an area of improvement, analyze the root causes, set up a plan with goals, and possible solutions.
- Implement the solutions.
- Find out if everything went as planned or, in other words, whether or not the goal was achieved. Potentially implementing new solutions.
- Reflect, act and standardize the results. Start a new improvement cycle.
This board is an excellent complement to your continuous improvement work.
Six Sigma
Six Sigma is a lean methodology for improvement work where the focus is on reducing errors and costs to create a process as good and profitable as possible.
Visualization boards can be of great benefit in more long-term Six Sigma projects. For example, with a Six Sigma customized board, you can work in-depth with detailed analyzes, perform improvements according to the Define Measure Analyze Implement Control (DMAIC) method, and support your project members by visualizing everything from progress, goals, analysis results, tests, tasks, and roles.
Risk board
With our unique risk boards, you can also identify and visualize opportunities and risks. By evaluating on likelihood and consequence, you get a risk number and can thus map out all potential outcomes in different areas of the business. These can then be aggregated up to the management, who gets a clear overview of where in the process the risks exist.
Work environment and safety
There’s always time to talk about safety in the workplace. The Safety Cross is basically a safety calendar and it's one of the most important tools in lean visual management. The calendar is shaped like a cross and you mark every accident free day green and the days when accidents occur with red. The idea is to keep it simple and clear, nobody wants to see a cross marked up in red.
Visibility of accidents and incidents at the workplace can have major effects in an improved safety behavior of your staff. Since accidents are marked with red in the Safety Cross model, everyone can see that something has happened. The information can also be enhanced by taking a picture with the mobile phone and attaching it to the report from the scene of the accident, so that everyone can become aware of which security risks exist in the workplace and also engage in eliminating them continuously.
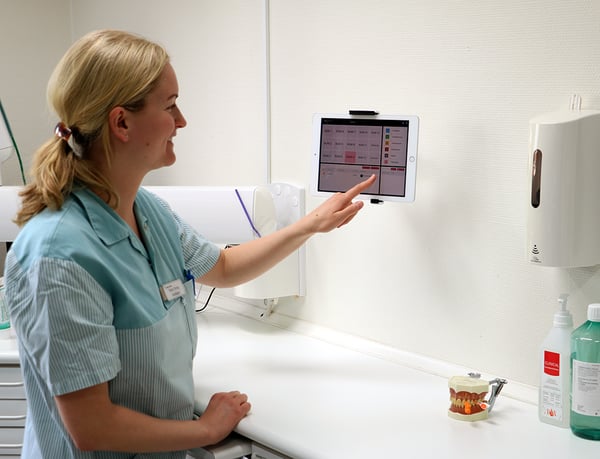
Patient safety with the digital Safety Cross
With the Safety Cross for patient safety, those who are responsible for a care department can digitally visualize injuries and risks in the same way as with accidents and incidents within the work environment. The Safety Cross for patient safety was one of the first things we developed in Mevisio, already in spring 2017 for two healthcare regions in Sweden, which probably makes it the world's first application of the digital Safety Cross for patient safety! In the cross, green means OK, and therefore you strive towards a green cross (instead of a red cross which normally stands for injuries and is also the symbol of the emergency reception).
5S-board
A common problem in many workplaces is that the environment is perceived as too messy. Too much time is lost when looking for tools, documents, etc. In the worst cases, the disorder can even pose a safety risk. Toyota's five S have been used successfully for decades to stabilize processes and create order and efficiency.
The method is based on five simple steps. With a digitized 5S board you can streamline and maintain the way you work and thereby ensure a safe workplace. You can also plan follow-ups and team 5S audits, and revise the various results continuously.
KPI, target management board
You can improve your daily management and daily operations by highlighting key figures and KPIs in a target visual management board, all employees can see how it goes for the business. It displays both current status and history for different targets and key figures, and visualizes the data in charts. If a goal is not achieved, you can easily add it as a new card to an improvement board.
Mevisio can be integrated with your current system, so working with Mevisio does not mean you have to start over. We simply compile and visualize the information that already exists. This allows you to hold effective meetings with live updated data and KPIs.
Hoshin Kanri, strategy deployment with the X matrix
Many companies find it difficult to visualize their long-term strategic plan in a way that is both easy to understand and visually appealing. No one likes to spend time reading long and complicated strategy plans. One way to avoid this is by implementing the Hoshin Kanri X Matrix.
Hoshin Kanri X Matrix is a planning tool that contains the entire company's strategic plan on a single page. Which makes it easy to see how overall strategies relate to improvement activities. The name comes from the X which divides the matrix into four parts and steps.
Part 1: Long-term goals
Part 2: Short-term goals
Part 3: Prioritization of improvement initiatives
Part 4: Measured values to improve
The Meviso team knows how crucial it is that the business's goals are clearly visualized, but also to create a system to lead the activities required to achieve the goals. Clear common goals combined with everyone knowing what is expected of them creates a corporate culture that breathes commitment.
Toyota Kata
A strong recommendation from us at Mevisio is that you implement Toyota Kata in your daily management. The concept is based on the idea that the management should take a step back to coach their employees, and teach them to help themselves. Instead of micro-managing them. You usually work with various "Kata initiatives' ' provided by the employees. These initiatives can easily be shared via the improvement board. This will help you take your continuous improvement work to the next level and create a corporate culture that "thinks lean". It's also a good idea to combine Toyota kata with the PDCA method.
Daily huddle board
A daily huddle is a short, recurring once-a-day meeting, held around a visual management board. The purpose of the meeting is to get control of the daily operations by aggregating and summarizing information from each team. A daily huddle board summarizes all the data you need to hold an efficient meeting. The goal is to make sure everybody is up to date and knows what needs to be done to reach the company goals. In Sweden we call it a Pulse board for the steady rhythm it creates and aims for.
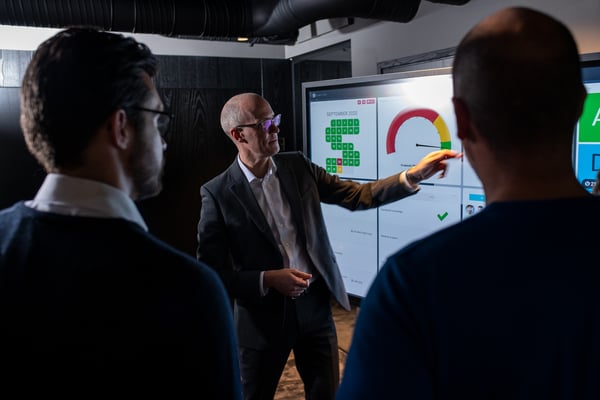
Kanban board
Kanban boards (or so-called Scrum boards or activity boards) are a very popular method for visualizing and streamlining processes. The activity board divides the process into different stages, which the jobs can then be moved between in small iterative development steps. This results in a more even development work with more ongoing deliveries.
All this, and much more, can be created in Mevisio—the digital platform for visualization and teamwork.
Do you want to know more about how get started with Mevisio? Read some tips about how to get started quickly here.
Discover how Mevisio aligns with your business goals
